ASK & WE ANSWER
frequently asked questions
Nabavite besplatni citat odmah!
Frequently Asked Questions
We’ve put together some commonly asked questions to give you more information about fertilizr production equipment we offer.
If you have a question that you can’t find the answer, please use the contact page!
Koliko košta 3T/H organska tvornica gnojiva u Malaviju?
PKladi se NPK visoke čvrstoće (Dušik, Fosfor, Kalij) Pelete gnojiva ključni su za poboljšanje poljoprivredne produktivnosti. Na Yushunxin, Profesionalni proizvođač opreme za gnojivo, Specijalizirani smo za pružanje naprednih rješenja za proizvodnju gnojiva. Postupak suhog granulacije NPK gnojiva, posebno pomoću dvostrukog granulatora, ključna je metoda za postizanje trajnih i ujednačenih peleta. U ovom članku, Istražujemo kako proizvesti NPK pelete visoke čvrstoće tehnikom suhe granulacije, Usredotočenost na važne čimbenike poput kontrole vlage, veličina čestica, pomoćni materijali, i optimizacija opreme.
Zašto je kontrola vlage važna u NPK suhoj granulaciji?
U postupku suhe granulacije NPK gnojiva, Kontroliranje sadržaja vlage u sirovinama je neophodno. Prekomjerni sadržaj vlage, obično gore 8%, može dovesti do blokade stroja u granulatoru dvostrukog valjka. Ovo pitanje ne samo da ometa učinkovitost proizvodnje, već i povećava troškove održavanja. S druge strane, Nedovoljan sadržaj vlage, Obično ispod 4%, mogu uzrokovati lako lomljenje peleta. Stoga, održavanje sadržaja vlage u idealnom rasponu 4% do 8% je presudno za proizvodnju peleta visoke snage.
68-200 KW dizelski generatori za opskrbu električnom energijom do 1-20 T/h Prašak organsko gnojivo Proizvodna linija
Na Yushunxin, Pružamo pomoćnu opremu koja pomaže u regulaciji razine vlage sirovina. Osiguravajući optimalni sadržaj vlage, Možete postići dosljedan postupak granulacije i poboljšati ukupnu kvalitetu NPK peleta. Štoviše, Pravilna kontrola vlage povećava performanse granulatora dvostrukog valjka, što dovodi do veće proizvodne učinkovitosti.
Kako veličina čestica utječe na kvalitetu peleta u granulaciji dvostrukog valjka?
Ujednačenost veličine čestica sirovina značajno utječe na kvalitetu peleta proizvedenih od strane granulatora s dvostrukim valjkama. Neravne veličine čestica mogu rezultirati nedosljednim stvaranjem peleta i smanjenom snagom. Izvođenjem odgovarajućeg prosijavanja, Možete osigurati da sirovine imaju jednoliku raspodjelu veličine čestica. Ova ujednačenost omogućava bolje sabijanje tijekom postupka granulacije.
Podešavanje tlaka valjka i jaz između valjka omogućuje proizvodnju peleta različitih veličina. Na primjer, Proizvodnja 3 mm peleta gnojiva vapna zahtijeva preciznu kontrolu ovih parametara. Dosljedna veličina čestica ne samo da poboljšava čvrstoću peleta, već također povećava raspodjelu hranjivih tvari u konačnom proizvodu. U našoj tvrtki, Naglašavamo važnost prilagođavanja veličine čestica u postizanju optimalnih rezultata u postupku suhe granulacije gnojiva NPK.
Koja je uloga pomoćnih materijala u poboljšanju čvrstoće peleta?
Dodavanje pomoćnih materijala igra vitalnu ulogu u povećanju snage i stabilnosti NPK peleta. Sredstva za vezanje poput bentonita i prirodne gline mogu se ugraditi u sirovu mješavinu kako bi se poboljšala kohezivnost. Ovi materijali poboljšavaju tvrdoću peleta, čineći ih otpornijima na lom tijekom rukovanja i prijevoza.
Pažljivim odabirom i dodavanjem odgovarajućih pomoćnih materijala, Možete značajno poboljšati kvalitetu peleta proizvedenih od zbijanja dvostrukog valjka. Naša stručnost u Yushunxin -u omogućava nam da savjetujemo najbolje pomoćne materijale za vaše određene sirovine i proizvodne ciljeve. Uključivanje ovih materijala ne samo da jača pelete, već i osigurava dosljedne performanse na terenu.
Kako optimizirati tlak i brzinu u granulatoru dvostrukog valjka?
Tlak i rotacijska brzina valjka u granulatoru dvostrukog valjka ključni su parametri koji utječu na kvalitetu peleta. Podešavanje tlaka utječe na stupanj sabijanja sirovina, što zauzvrat utječe na gustoću i snagu peleta. Veći pritisak općenito dovodi do jačih peleta, Ali pretjerani pritisak može uzrokovati nepotrebno trošenje opreme.
Slično, Brzina valjka određuje vrijeme boravka materijala unutar granulatora i utječe na stopu proizvodnje. Optimiziranjem tlaka i brzine, Možete kontrolirati kvalitetu i veličinu peleta. Naši dvostruki valjak granulatori dizajnirani su s podesivim postavkama, omogućujući vam da fino podešavate operaciju na temelju karakteristika vaših sirovina. Ova fleksibilnost osigurava da postignete željenu kvalitetu peleta uz održavanje učinkovitih stope proizvodnje.
Sažetak, Proizvodnja NPK peleta visoke čvrstoće tehnikom suhe granulacije uključuje pažljivo razmatranje nekoliko tehničkih čimbenika. Kontrola vlage ključna je za sprečavanje blokade stroja i loma peleta. Podešavanje veličine čestica kroz postavke prosijavanja i valjka dovodi do ujednačenih i visokokvalitetnih peleta. Uključivanje pomoćnih materijala poput bentonita i prirodne gline pojačava čvrstoću i stabilnost peleta. Konačno, Optimiziranje tlaka i brzine dvostrukog granulatora valjka omogućuje precizno upravljanje svojstvima peleta.
Ponuda dovoljno snage za proizvodnju gnojiva značajna je briga, posebno u regijama s nestabilnom opskrbom električnom energijom. Radom s Yushunxin, Predlažemo da kupite našu naprednu opremu za gnojivo s dizelskim generatorom, moguće je ispuniti zahtjeve za napajanjem učinkovito. Nadalje, Naša tvrtka pruža ne samo visokokvalitetnu opremu za proizvodnju gnojiva, već i sveobuhvatna rješenja za osiguranje pouzdanog i ekonomičnog napajanja napajanja.
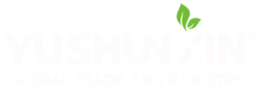
Nabavite besplatni citat odmah!
Koliko košta 3T/H organska tvornica gnojiva u Malaviju?
Many of our customers in regions like the Middle East and Africa face challenges with electricity supply. Štoviše, they often face issues like power shortages, high electricity costs, or unstable supply, particularly for their fertilizer factories in rural or mountainous areas. They hope that, while we provide information on fertilizer production equipment, we also consider energy issues and offer effective solutions. Thus, we, as a professional fertilizer equipment manufacturer, have devised a reasonable solution to address these concerns about both the power needs and the equipment specifications. Zapravo, by utilizing diesel generators to provide the necessary power for fertilizer production process, and taking advantage of generally low dizel prices, it’s a practical approach.
How Much Power Does Organic Fertilizer Production Require?
Organic fertilizer production lines can vary greatly in power needs depending on their scale. Također, if you want to make powdered organic fertilizers than organic fertilizer pellets, you may need less power requirement. According to 1-20 t/h organic fertilizer manufacturing process, its power is within 30-400 kW. So we offer different diesel generators for you needs. Na primjer:
68-200 KW dizelski generatori za opskrbu električnom energijom do 1-20 T/h Prašak organsko gnojivo Proizvodna linija
Tipično, the main processes of a powder organic fertilizer production line include fermentation, drobljenje, ekraning, mixing, i pakiranje. Since it’s relatively simple, the power demand is comparatively low. Na primjer,
A small-scale fertilizer plant producing 1-3 t/h of organic fertilizer powder requires approx. 30-50 kW of power. So you can meet this electricity need by equipping a diesel generator with an output power of 68 kW.
Naduti, medium-scale organic fertilizer factory producing 5-10 Tone/sat powder will require at least 100 kW of power. A diesel engine with an output power of 150 kW is suitable in this case.
Dodatno, a large-scale organic fertilizer powder production plan (20 t/h) requires at least 150 kW of power, requiring a diesel generator with 200 kW output.
What Is the Power Demand for 1-20 TPH NPK Fertilizer Granule Production?
Granular organic fertilizer production lines involve additional processes like granulation, drying, and cooling, increasing power demand.
Generally, a 1-5 Tone/sat organic fertilizer granulation line requires around 100 kW, with a diesel engine output of 150 kW.
Uz to, the 8-10 t/h granular organic fertilizer production proposal requires around 200 kW of power, and a diesel generator with an output power of 300 kW is appropriate.
For large fertilizer manufacturers to produce 15-20 t/h organic fertilizer granules, the total power will range from 300-400 kW. A diesel generator with an output power of 400-500 kW can fulfill this requirement.
What Are The Power Solutions for 5-80 T/h BB Fertilizer Production?
A bulk blend fertilizer plant layout include material feeding system, conveyors, batching and weighing system, mixing system, and packaging system. For one thing, the common bulk mixing fertilizer production line producing 1-15 t/h of bb fertilizer, the power requirement is about 30-100 kW. A generator with a diesel engine output of 50-150 kW can meet these power demands. For the largest bulk blended fertilizer manufacturing process (50-80 t/h), power needs increase to 200-300 kW, requiring a diesel generator with output of 300-400 kW.
What Is The Power Demand for 1-20 TPH NPK Fertilizer Granule Production?
A 1-20 t/h NPK fertilizer factory equipment configurations may include batching machine, drobilica, mikser, granulator, sušilica, hladnjak, stroj za provjeru, and bagging machine, itd. The complexity and automation level of the compound fertilizer manufacturing process influence the equipment’s power demand. For various NPK fertilizer production capacities:
A small-scale NPK fertilizer production line (1-8 Tone/sat) requires about 80-150 kW, with a diesel generator output of 120-200 kW.
A medium-scale compound fertilizer granulation line (10-15 t/h) has a total power of 200-300 kW, necessitating a diesel generator with output powers of 300-400 kW.
Large npk fertilizer factory (25-40 t/h) will need 400-600 kW of power, and we recommend a diesel engine with 500-800 kW output.
Technical Parameters of Diesel Generators for Fertilizer Manufacturing
Model | Output Power (KW) | Engine Model | Engine Power | Cylinder | Bore/Stroke (mm) | Discharge (L) | Size (L*W*H) | Weight (kg) |
SXCF-30 | 30 | YT3B2-D | 40 | 3 | 105/120 | 3.3 | 1800*670*1400 | 670 |
SXCF-50 | 50 | YT4B2Z-D | 65 | 4 | 108/125 | 4.76 | 2000*780*1220 | 1040 |
SXCF-68 | 68 | TD520GE | 83 | 4 | 108/125 | 4.76 | 2080*680*1450 | 1150 |
SXCF-80 | 80 | TAD531GE | 100 | 4 | 108/125 | 4.95 | 2150*750*1450 | 1200 |
SXCF-100 | 100 | LR6A3L-D | 130 | 6 | 108/130 | 6.49 | 2200*750*1450 | 1300 |
SXCF-120 | 120 | LR6B3L-DA | 160 | 6 | 108/130 | 6.49 | 2400*870*1450 | 1380 |
SXCF-150 | 150 | LR6M3L-DA | 200 | 6 | 108/130 | 6.87 | 2550*1000*1450 | 1600 |
SXCF-200 | 200 | TAD733GE | 300 | 6 | 120/135 | 7.15 | 2600*1020*1500 | 1750 |
SXCF-250 | 250 | TAD734GE | 340 | 6 | 120/135 | 7.15 | 2800*1100*1500 | 1850 |
SXCF-300 | 300 | TAD941GE | 400 | 6 | 126/150 | 8.82 | 3000*1100*1560 | 1900 |
SXCF-350 | 350 | TAD1241GE | 470 | 6 | 126/150 | 9.76 | 3050*1120*1560 | 1950 |
SXCF-400 | 400 | TAD1242GE | 520 | 6 | 126/150 | 12.1 | 3100*1150*1600 | 2100 |
SXCF-450 | 450 | TAD1641GE | 590 | 6 | 144/165 | 16.12 | 3200*1200*1650 | 2500 |
SXCF-500 | 500 | TAD1642GE | 650 | 6 | 144/165 | 16.12 | 3300*1250*1700 | 2700 |
How to Optimize Power Consumption for Fertilizer Production?
Fertilizer equipment model differences can affect power demands since different fertilizer machinery manufacturers and models may have varying specifications. When selecting equipment, it is essential to consider specific fertilizer equipment parameters when selecting machinery to ensure power efficiency.
Naduti, energy consumption optimization is crucial. Our equipment features energy-saving designs. And the actual running power may be lower than the installed power. This can reduce operational costs while maintaining high performance.
Dodatno, process configurations, such as the addition of extra steps like pre-treatment or secondary fermentation can impact the overall power requirements. To ensure the stable operation of the organic or compound fertilizer production line, it is necessary to consider the capacity of the power supply lines and reserve a certain margin.
FAQ
How to Get A Good Power Solution from A Proizvođač opreme za gnojivo?
Consulting the equipment supplier is a vital step. We, at Yushunxin, can offer customizable power solutions based on your specific fertilizer production line and equipment configuration. In fertilizer equipment selection and process design, we consider using high-efficiency, energy-saving fertilizer production machines and technologies to reduce energy consumption. Of course, you can also buy single fertilizer making machinery equipped with a small diesel generator.
Consulting the equipment supplier is a vital step. We, at Yushunxin, can offer customizable power solutions based on your specific fertilizer production line and equipment configuration. In fertilizer equipment selection and process design, we consider using high-efficiency, energy-saving fertilizer production machines and technologies to reduce energy consumption. Of course, you can also buy single fertilizer making machinery equipped with a small diesel generator.
Ponuda dovoljno snage za proizvodnju gnojiva značajna je briga, posebno u regijama s nestabilnom opskrbom električnom energijom. Radom s Yushunxin, Predlažemo da kupite našu naprednu opremu za gnojivo s dizelskim generatorom, moguće je ispuniti zahtjeve za napajanjem učinkovito. Nadalje, Naša tvrtka pruža ne samo visokokvalitetnu opremu za proizvodnju gnojiva, već i sveobuhvatna rješenja za osiguranje pouzdanog i ekonomičnog napajanja napajanja.
Ponuda dovoljno snage za proizvodnju gnojiva značajna je briga, posebno u regijama s nestabilnom opskrbom električnom energijom. Radom s Yushunxin, Predlažemo da kupite našu naprednu opremu za gnojivo s dizelskim generatorom, moguće je ispuniti zahtjeve za napajanjem učinkovito. Nadalje, Naša tvrtka pruža ne samo visokokvalitetnu opremu za proizvodnju gnojiva, već i sveobuhvatna rješenja za osiguranje pouzdanog i ekonomičnog napajanja napajanja.
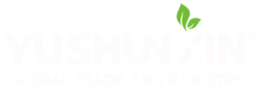
Nabavite besplatni citat odmah!
How to Compost Chicken Manure in 18 Days?
Recently, our company has received many customers’ inquiries in poultry farms or organic fertilizer plants. They are very concerned about the equipment and process for composting chicken manure. Here, we provide a comprehensive guide on how to compost chicken manure in 18 days, focusing on the necessary equipment, raw materials, and specific steps involved.
Nabavite besplatni citat odmah!
What Raw Materials Are Needed for Chicken Manure Composting?
Doista, chicken dung is rich in nitrogen and an essential raw material in organic fertilizer production. Composting chicken manure requires a balance of materials to create an optimal environment for decomposition. Tipično, maintaining the right C/N ratio in composting process, between 25:1 i 30:1, is crucial for effective composting. Uz to, adding carbon sources like rice husk, corn straw, or sawdust helps balance the C/N ratio. Štoviše, you can use fermentation bacteria for organic matter quick decomposition. Bacillus subtilis and Bacillus licheniformis are commonly of use to accelerate the composting process.
What Jas The Process of Composting Chicken Dung Over 18 Days?
Composting chicken manure involves several steps to ensure the process is efficient and effective. We have summarized the basic day-by-day operation procedure based on the feedback of different customers to their chicken manure composting process.
Day 1-3
Prvo, it’s important to reduce the chicken manure moisture. At the beginning, chicken dung has about 80% voda. Thus, a dewatering machine can reduce moisture down to 50-60%. Dodatno, you can collect chicken manure and carbon sources to achieve the optimal C/N ratio. You need to add fermentation bacteria to facilitate chicken dung decomposition. Osim toga, you must pile the materials in a suitable composting area, ensuring good ventilation.
Day 4-7
Secondly, during the chicken manure fermentation process, you must monitor the temperature closely. Štoviše, the best fermentation temperature range is 60-70℃. When the temperature naturally exceeds 70℃, you can choose a suitable composting equipment to turn the pile for maintaining aeration and even decomposition.
Day 8-10
Thirdly, you need to continue monitoring the temperature and moisture of compost piles in this stage. The decomposition rate will be high during this phase, and the pile will produce a significant amount of heat. If it’s necessary, you can increase turn frequency of compost piles. Također, if it becomes too dry, you should add water at a certain degree.
Day 11-14
Fourthly, after the 11th day, the temperature of composts may start to stabilize. Sigurno, you should keep turning the pile by the compost turner to maintain aeration and moisture at an excellent level. If any foul odors appear, which indicate anaerobic conditions, you must turn the piles more frequently to ensure complete decomposition and uniform mixtures.
Day 15-18
By now, the compost should be mature, with a stable temperature and a crumbly texture. At this time, the moisture content of chicken manure compost should be around 25-30%. Konačno, the compost is now ready for the next handling process.
What Equipment Are Essential for Composting Chicken Manure Efficiently?
A screw dehydrator is essential for reducing the moisture content in chicken manure before composting. This machine effectively removes excess water, ensuring optimal conditions for the composting process. With durable stainless steel construction, the dewatering machine offers consistent performance and longevity, making it a reliable choice for efficient manure management.
Selecting the right composting machine is crucial for efficient composting. We offer seven types of compost turners. Our composting solutions include groove type turners with customizable depths, wheel and chain plate turners for large-scale operations, and moving and crawler type turners for versatility. We also offer horizontal fermenters for fast processing and vertical fermenters for limited space, though higher cost makes them less ideal.
Naduti, we can customize an optional water spray system for each compost plans to provide moisture during the composting process. Hence, these machines provide efficient solutions for producing high-quality organic fertilizer powder or granules from chicken manure.
How Do You Know When Chicken Manure Composting Jas Complete?
The composting process from chicken manure is complete when appearing several identifiable characteristics:
Temperature Stabilization: The temperature of the pile stabilizes and no longer heats up after turning.
Compost Texture: The chicken dunghas a dark, crumbly texture similar to soil without other recognizable materials.
Smell: There is no offensive odor. Također, it smells like earthy, free from ammonia or foul odors.
Moisture Content: The final product should have a moisture content of 25-30%.
Composting chicken manure in 18 days is available with the right equipment and process management. Our fertilizer production machines offer cost-efficient and effective solutions for every customer. By following these steps and monitoring key factors, you can produce high-quality chicken dung compost efficiently. As a professional fertilizer equipment manufacturer, Yushunxin is committed to providing the best solutions for your composting needs.
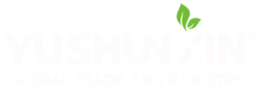
Nabavite besplatni citat odmah!
When you choose our series of granulators, you have the flexibility to select the shape of the granules according to your specific needs. We can produce a variety of shapes including pillow shape, semicircle shape, stick shape, pill shape, walnut shape, flat ball shape, and square bar shape. Štoviše, the roller press granulating machine will be your ideal solution. This variety ensures that you can find the perfect match for your project requirements.
Nabavite besplatni citat odmah!
What Shape of Granules Can You Get From YSX Roller Granulating Machine?
When you choose our series of granulators, you have the flexibility to select the shape of the granules according to your specific needs. We can produce a variety of shapes including pillow shape, semicircle shape, stick shape, pill shape, walnut shape, flat ball shape, and square bar shape. Štoviše, the roller press granulating machine will be your ideal solution. This variety ensures that you can find the perfect match for your project requirements.
How Does The Shape Selection Process Work before Granulation?
As a customer, you play a pivotal role in the shape selection process. Initially, you will communicate your preference based on the application for which the granules are intended. Our team from Jushunxin will then guide you through the options, helping you understand the implications of each shape for your project. Once a decision is made, we customize the ball socket on the roller sheet to produce granules in your chosen shape.
Can the Size of the Granules Be Customized?
Yes, alongside the shape, the size of the granules can also be tailored to meet your needs. Uz to, we can customize molds for the production of 3-10mm diameter particles, and even larger industrial machine ball shape press granulator can produce pellets in excess of 10mm. Thus, the customization of both aspects is a testament to the flexibility our granulators offer. So, this ensures you receive a product that perfectly aligns with the specifications of your application, enhancing the efficiency and quality of your end products.
What Advantages Do Different Granule Shapes Offer by YSX Granulator?
Different shapes offer unique advantages depending on the application. Na primjer, pillow-shaped granules might be ideal for certain types of fertilizers, providing excellent dispersal properties. Semicircle and stick shapes may be preferred in feed industry for ease of swallowing. Our expertise lies in matching the shape and size of the granules to the intended use, ensuring optimal performance.
How Can We Guarantee Our Granulator Meeting Your Pelletizing Requirements?
To fulfill your specific shape and size requirements, we recommend reaching out to our customer service team. We will engage in a thorough consultation process, understanding your project needs and advising on the best granule shapes and sizes. Afterward, we customize your unique granulating machine to meet these specifications. And before delivery will be a trial run, we can produce the corresponding particle samples and take photos for customer trust.
In conclusion, our series of double roller compact granulators offers unparalleled flexibility in the production of granules, with a wide range of shapes and sizes available to suit your specific needs. By collaborating closely with our team, you can ensure that the granules you make are perfectly adapted to your application, contributing to the success of your projects.
Dry roller press granulator, also known as extrusion granulator, offers several advantages that make it a preferred choice in the fertilizer production industry or other industries. Štoviše, as a professional equipment manufacturer in China, Jushunxin ensures that our clients experience the pinnacle of efficiency and quality. Here are some of its key features:
Nabavite besplatni citat odmah!
1. Energy Saving & Consumption Reduction
One of the major advantages of the dry roller press granulator is its energy-saving and consumption reduction capability. Unlike other methods, this granulation process takes place at room temperature without the need for drying. So you can eliminate the need for drying processes that typically consume substantial amounts of fuel or gas. Zatim, you benefit from a significant energy savings, aligning with the contemporary need for sustainable production practices.
2. No Need for Another Binder
The dry granulation process featuring the roller press granulator eliminates the need for another binder. Our technology simplifies the granulation process by leveraging the material’s intrinsic inter-molecular forces, negating the necessity for additional binders. This not only streamlines the production process but also reduces the overall cost of production.
3. Cost-Effectiveness & Low Investment
The elimination of the drying process in dry roller press granulation results in several cost-saving benefits. The absence of return material, one-step forming, and low noise make the system simple to operate and maintain, thereby reducing investment costs. This makes the dry roller press granulator a cost-effective choice for fertilizer production, translates into significant savings in terms of both time and money.
3. Flexibility in Raw Material Composition
The extrusion granulation production method offers a wide range of flexibility in terms of raw material composition. It can process different types and concentrations of compound fertilizer. Naduti, the extrusion granulation process allows for quick product formulation replacement, enabling a set of devices to handle several product formulations within a short period of time.
5. Commitment to Environmental Protection
The dry roller press granulator operates on electricity as its driving force, resulting in no three waste emissions. This aligns with the growing emphasis on environmental protection in enterprises. By employing the granulator, businesses can comply with environmental regulations while maintaining their production efficiency.
6. Long service life
Durability is a hallmark of our granulator, with key components such as the frame constructed from new, corrosion-resistant metals. The bearing frame body is crafted from high-quality, anti-corrosion materials, enhancing stability and extending the service life of the rolling bearings. This guarantees durability and reliability, reducing maintenance costs in the long run.
In conclusion, the dry roller press granulator offers advantages such as energy-saving and consumption reduction, no need for another binder, low cost and investment, flexible composition of raw materials, environmental protection, and long service life. It is a reliable and efficient choice for fertilizer production. And it is a comprehensive solution designed to enhance productivity, sustainability, and efficiency in your production processes.
The engine we use in our fertilizer production equipment, more specifically in crushers, mixers, rotary screening machines, rotary drum dryers and packing machines, are primarily electric. Uz to, we’ve found that electric motors tend to offer smoother and more efficient operation, require less maintenance, and are more environmentally friendly compared to diesel engines. Štoviše, our composters are available in two drive forms, with three options for electric and two for diesel.
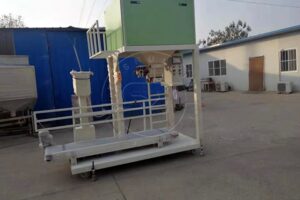
Single Bucket Packing Scale
Na primjer, consider our electric packaging machines. They are designed for swift, precise, and energy-efficient operation. The electric engine ensures consistent performance, reducing the risk of downtime. They also offer quieter operation, improving the working environment by reducing noise pollution.
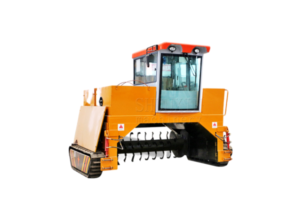
Crawler Compost Equipment for Sale
S druge strane, we understand that specific scenarios might necessitate the use of a diesel engine. Take our diesel-powered crawler compost turner as an example. This machine is praised for its robustness and high torque, perfect for heavy-duty tasks. Diesel engines are also renowned for their durability and long service life, making them a cost-effective solution in the long run. Štoviše, a diesel engine provides more power, which is advantageous in the rough terrains often encountered in agriculture and farming.
Međutim, we understand that some clients might prefer or need a diesel engine. If this is the case for you, we are more than willing to engage in a dialogue and explore possible alternatives to ensure that we meet your specific needs. We are keen on providing equipment that not only meets your functional needs but also aligns with your environmental and sustainability goals. Rest assured, our team of experts will work tirelessly to cater to all your requirements. If you have any more queries or need further customization, our customer service team is always on standby to assist you.
The engine we apply in our fertilizer production equipment is fundamentally an electric motor from a conventional Chinese brand. We’ve chosen this motor based on its commendable performance, undisputed reliability, and the ability to function optimally under diverse operational conditions. Uz to, these motors have been tried and tested to ensure they meet stringent quality control standards and deliver consistent results.
We recognize, however, that different clients have different preferences and specific needs. Stoga, we have made a provision to offer a customization option. If you prefer an internationally recognized brand such as Siemens, we can facilitate this change for you. While the change to Siemens or any other global brand of your choice might result in a slight additional cost, we want to assure you that it’s all aimed at ensuring that your equipment aligns perfectly with your individual specifications and standards.
Please note that opting for customization might slightly adjust the delivery schedule of your equipment. Nonetheless, we assure you that the quality, performance, and efficiency of your equipment will in no way be compromised.
Our BB fertilizer mixer is compatible with granule materials, including NPK fertilizers. It processes material quickly, with a turnaround time of 3-5 minutes, and can even produce final material in as little as 40 seconds. With a capacity of 5-10 tons per hour, it meets various production needs. The price is all-inclusive, covering the feed hopper, main cylinder, and essential accessories like the motor and control cabinet. Its efficient discharge system operates by forward rotation for feeding and reverse for discharging.
Our compost crusher is specifically designed for materials that have undergone the fermentation process. For unfermented raw materials, the crusher can still be used directly, provided that the moisture content is between 20-40%. The typical output size from the semi-wet material crusher is about 5-8mm. If a smaller size is required, we recommend using the straw crusher, which includes an internal screen to achieve a finer crush. Međutim, ensure that the moisture content of the materials for the straw crusher does not exceed 15%.
Before granulation, it is essential to ensure that the moisture content of the raw material is around 30%. After granulation, the moisture content of the granules is about 20%. If you require a moisture content below 10%, you can utilize a rotary drum dryer to reduce the moisture content accordingly.
Our organic fertilizer production line equipment is primarily constructed from boiler steel (Q235B), with certain parts crafted from standard carbon steel. For the packing machine specifically, stainless steel is used for the interior. The thickness of the iron components varies by machine and model but is in compliance with national standards. In terms of durability, you can expect a life expectancy of 8 do 10 years from our equipment, although this can vary based on maintenance routines, operating conditions, and general care.
The moving type compost turner is designed with a motor that operates efficiently with water. The machine is equipped with a water tank where water should be added for optimal functionality. It features a fan-based refrigeration system that helps in maintaining the motor’s temperature during operation. When it comes to fuel, the machine uses diesel oil, which is readily available and convenient. For lubrication purposes, normal butter can be applied to ensure smooth operation of the moving parts. In terms of fuel efficiency, the compost turner consumes approximately 8 liters of diesel per hour, making it economically viable for continuous operation during compost turning processes.