Fertilizer Manufacturing Plant Cost
What calls for special attention for entrepreneurs and investors interested in establishing a fertilizer manufacturing plant is that understanding the cost factors. If you’re looking for information on the fertilizer manufacturing plant cost, it involves expenses such as land rent, plant construction, fertilizer production equipment, raw and auxiliary material costs, labor costs, energy consumption, etc. Typically, according to raw materials and output, we can customize different fertilizer production solutions for customers’ organic fertilizer, compound fertilizer, bulk blending fertilizer or liquid fertilizer production factories, for clients with equipment budgets ranging from $10,000 to $1,200,000.
What calls for special attention for entrepreneurs and investors interested in establishing a fertilizer manufacturing plant is that understanding the cost factors. If you’re looking for information on the fertilizer manufacturing plant cost, it involves expenses such as land rent, plant construction, fertilizer production equipment, raw and auxiliary material costs, labor costs, energy consumption, etc. Typically, according to raw materials and output, we can customize different fertilizer production solutions for customers’ organic fertilizer, compound fertilizer, bulk blending fertilizer or liquid fertilizer production factories, for clients with equipment budgets ranging from $10,000 to $1,200,000.
How Much Does It Cost to Set up An Organic Fertilizer Plant?
Are you considering setting up an organic fertilizer plant? Our company offers affordable organic fertilizer manufacturing plans ranging from 1-20 t/h capacity. The organic fertilizer plant cost depends on the production scale and fertilizer type. Consequently, you can choose a cost-effective simple powder organic fertilizer line under $10,000. Or a large granule organic fertilizer production line costs up to $550,000, which has higher demand in fertilizer market due to better appearance and quality. Whether starting a small or planning a big organic fertilizer business plan, we offer different pricing options to choose from.
1-20 T/H Business Plan for Powder Organic Fertilizer Factory
f you seek building a cost-effective organic fertilizer factory, we recommend investing in a powder organic fertilizer line. Because this simple method requires fewer fertilizer machines and lower organic fertilizer plant cost. Our company can customize powdery organic fertilizer production solution ranging from 1-20 t/h, with budgets within $90,000. Typically, you can set up a complete organic powder fertilizer plant, including essential equipment such as a composter, feeder, crusher, screening machine, buffer bin, packing machine, and belt conveyors.
1-20 T/H Granular Organic Fertilizer Plant Project
Granular organic fertilizer is in higher demand than powder fertilizer due to its attractive appearance and superior quality. If you intend to start an industrial organic fertilizer plant, we can customize 1-20 t/h organic fertilizer production solutions. Such an organic fertilizer plant cost varies between $100,000 and $550,000. Unlike powder fertilizer, our granular organic fertilizer production process is more complex. It includes composting, feeding, shredding, mixing, granulation, screening, packaging, and conveyor systems. Also, it requires additional units such as drying, cooling, and dust removal. Even adding a coating or polishing machine can enhance product appearance and prolong storage life. Therefore, the initial organic fertilizer pellet plant investment is higher than a powder organic fertilizer factory. Of course, we have more complete organic fertilizer granule manufacturing plans for your needs.
20,000 USD Simple Granular Organic Fertilizer Making Plan
In fact, if you don’t have enough money, our company offers an economical 1-2 t/h organic fertilizer granulation solution costing under $20,000. This organic fertilizer plant setup includes a 2400 crawler compost turner, a 1212 feeding machine, a 600 vertical crusher, a 1040 rotary screener, and a packing scale with five 6-10 m belt conveyors. Moreover, you can choose either a 1800 disc granulator for spherical granules or a 400 flat die granulator for columnar shapes. However, since these organic granules contain certain moisture during this simple organic fertilizer granulation process, natural drying is necessary before sale. Thus, this low-cost solution is ideal for small-scale organic fertilizer producers seeking an affordable fertilizer pellet making proposal.
1-5 TPH Granular Organic Fertilizer Factory Investment
Generally, if you wish to produce 1-5 t/h of organic fertilizer pellets, we recommend purchasing a manure dehydrator, 3000 crawler-type compost turner and a churning granulator or pan pelletizer. And other auxiliary equipment should select small models matching the 1-5 t/h capacity. Therefore, the organic fertilizer factory cost for this setup is within $100,000–200,000, providing a balance of cost and quality.
8-10 T/H Organic Fertilizer Granulation Line Price
If your budget is around $250,000 to $360,000, you can opt for an 8-10 t/h granular organic fertilizer production line. We recommend choosing a groove type compost turner along with necessary auxiliary equipment from crushing, mixing to packing. Most importantly, you’d better to purchase the 2080 rotary drum granulator, with the capacity of 8-15 t/h. And you can add a pan granulator to enhance the organic fertilizer granule roundness.
Price of 15-20 TPH Organic Fertilizer Granule Factory Setup
If you run a large organic fertilizer production enterprise, you can consider a 15-20 t/h organic fertilizer granulation line is ideal. Its total equipment cost is around 400,000 to 550,000 dollars. In addition, we suggest you buy a double wheel compost turner. Indeed, you will need to purchase the largest model 3210 drum granulator and two 3600 disc pelletizers, enhancing the finished granulation rate. Then, equipping two dryers in 20 t/h organic fertilizer production process will improve drying efficiency. All auxiliary equipment should be the largest models, and a double-hopper bagging machine will meet the needs of large-scale production.
What Is A Compound Fertilizer Manufacturing Plant Cost?
When you consider investing in a compound fertilizer plant, the cost varies based on your production needs and budget. We offer many solutions ranging from $20,000 to $500,000, depending on capacity and technology. For startups, you might opt for a simple NPK powder batching line, producing 10-20 t/h compound powder. Addtionally, starting a BB fertilizer production plant with low cost offers a alternative option for 5-15 tons/hour capacity. If you have enough money, you can invest in large scale NPK granulation plants with the capacity up to 40 t/h.
Compound Powder Fertilizer Plant Design
Due to the affordable cost and easy availability of NPK powder raw materials, our company offers the most cost-effective NPK compound fertilizer production plan for clients. We recommend investing in an NPK powder batching line with a budget of 20,000-30,000 USD, achieving an hourly output of 10-20 tons. This solution requires fewer machines and occupies less space, reducing land and equipment costs, ideal for many compound fertilizer suppliers aiming for quick profits.
Regularly, the essential equipment includes a 2030 feeding machine, vertical crusher, 8030 double shaft mixer, powder packing scale, and five B500 belt conveyors. Moreover, you can choose between 3-4 bin static or dynamic blending machine depending on your NPK fertilizer formula, such as 15-15-15, 20-10-10, or 10-20-20. This design ensures precise NPK compounds mixing and low NPK fertilizer plant cost.
1-40 T/H Simple NPK Blending Fertilizer Factory
Relatively speaking, we highly recommend investing in a BB fertilizer factory solution to new factory owners. Because the bulk blending fertilizer production process is quite simple. It usually involves batching machine, rotary mixer, and other equipment. In other words, this bulk blended fertilizer production line focuses highly on the mixing process. So you can apply a cost-effective bb fertilizer production solution to reduce equipment, land construction, energy cost, etc.
In general, a basic bb fertilizer production line with a capacity of 5-15 tons per hour. Typically, it requires a static or dynamic batching machine with 3 or 4 bins, small BB fertilizer mixer, bucket elevator, and an automatic packing scale. The cost of such a NPK fertilizer mixing plant is about $30,000 to $50,000, making it affordable for most startups.
Moreover, investing an NPK fertilizer blending line is suitable for those fertilizer businesses wishing to expand their fertilizer product types. Because bulk blending fertilizer plant allows you to meet diverse fertilizer market demands through flexible NPK formulas. In addition, we can design a custom BB fertilizer plant layout to suit your budget.
Notably, if you want to expand the NPK fertilizer production scale, we can design bb fertilizer factory layout with the capacity of 20-40 t/h. And this npk fertilizer mixing project will cost about $70,000 to $100,000. Besides, you ought to buy a dynamic batching machine with 6-8 bins, large drum fertilizer blender, three-way distributor, two double-hopper particle packing scales, and four conveyors.
1-30 TPH Compound Fertilizer Pellet Plant
Customers interested in establishing NPK fertilizer granulation plants often possess fertilizer industry experience. Whether you want to scale up your compound fertilizer production business to make more profits or seek to achieve commercial NPK fertilizer pellet manufacturing while maintaining environmental compliance. Our company offers customized 1-40 t/h granular compound fertilizer production solutions, utilizing two main NPK granulation technologies: dry granulation and wet granulation.
What Is The Liquid Fertilizer Production Line Price?
Nowadays, many agricultural enterprises seek more eco-friendly and efficient fertilizer solutions to to meet modern farming demands. Therefore, we offer corresponding liquid fertilizer production projects for both organic and NPK liquid fertilizers. The cost of a liquid fertilizer production line is somewhat high because almost all the equipment is made of stainless steel. Consequently, it ensures durability and resistance to corrosion during the fertilizer liquid production.
What Is Budget to Buy Liquid Fertilizer Equipment?
Indeed, the standard liquid fertilizer production process integrates batching, mixing, fermentation, chelation, storage, filling, and palletizing. We can customize liquid fertilizer production lines with capacities ranging from 1,000 L/h to 20,000 L/h. Depending on the specific production capacity and configuration, the liquid fertilizer plant equipment cost basically ranges between $50,000 and $300,000.
What Is The Difference Between Organic Or NPK Liquid Fertilizer Production Plant?
Of course, if you need other equipment such as water purification ultrafiltration membranes, water pumps, and flow meters, you can contact us. We will provide more detailed equipment parameters and quotations for your liquid fertilizer factory. Also, our liquid fertilizer equipment boasts high durability, precision, and low maintenance requirements.
What Is The Land Cost to Establish A Fertilizer Plant?
Establishing a fertilizer plant involves various factors, you must assess land requirements and regional pricing. Whether setting up an organic, NPK, or liquid fertilizer production line, we provide free design of fertilizer plant layout drawings, including 3D designs and CAD services or on-site inspections. Typically, you should allocate 20-30% extra space for raw material storage and finished fertilizer warehousing. Based on our global customer data, land rent ranges $5–30 per square meter per year, while purchasing land costs between $100-500 per square meter.
An organic fertilizer factory producing 5,000 to over 100,000 tons annually generally requires a total area of 1,000-15,000㎡. Moreover, we can design 1-20 t/h organic fertilizer production lines, typically occupying 800-10,000㎡. Therefore, we estimate your land cost for an organic fertilizer plant ranges from $5,000 to $300,000 per year for leasing, or $100,000 to $6 million for purchasing. If your production site is limited, you can choose a powder organic fertilizer manufacturing process to reduce construction needs by 40-50% since granulation workshops are unnecessary. Additionally, we offer most economical options, such as simplest powder or granule organic fertilizer production line, requiring as little as 200㎡. Thus, land rent for these minimal organic fertilizer factory setups may cost $1,000-5,000 annually, while purchasing the land may cost 20,000-90,000 USD.
The demand for compound fertilizers is substantial in the market. Our conventional NPK fertilizer production lines can meet 1-40 t/h fertilizer production needs. Also, we estimate that a compound fertilizer plant requires a total area of 1,000-8,000㎡. Accordingly, the land cost ranges from $5,000 to $240,000 per year for leasing, or 100,000 to 4 million dollars for purchasing. If your land budget is not enough, we recommend dry compound fertilizer granulation plans, saving 30–40% space of NPK fertilizer plant. Alternatively, you can choose an NPK fertilizer mixing line, reducing land use by 50%. We also have the smallest NPK fertilizer production line layout plans. Whether you want to produce compound powders, bb fertilizers or NPK pellets, it only need 500 square meters. Thus, you need about annual land rent of $2,500-15,000 or 50,000-250,000 USD for purchasing industrial land to build a compound fertilizer factory.
Furthermore, we can customize 1,000-20,000 L/h liquid fertilizer manufacturing line. In addition, we estimate land requirements of 1,000 to 5,000 square meters to set up a liquid fertilizer plant. Consequently, you may pay approximately $5,000 to $50,000 per year to rent a liquid fertilizer plant, or prepare $100,000 to 2.5 million dollars to purchase it.
In fact, the actual liquid fertilizer production area depends on the production process, equipment type, and facility layouts. Additionally, an organic liquid fertilizer plant requires about 20% more area than an NPK liquid fertilizer factory. This is because the former needs to establish a large sedimentation tank and additional dehydration and filtration equipment.
Our company provides customizable layout designs and cost-effective solutions for fertilizer plant setups. With our expertise, you can minimize land costs while optimizing fertilizer plant efficiency. You can contact us to learn more about fertilizer plant construction information.
Buying Yushunxin Fertilizer Equipment to Save Labor Cost for A Fertilizer Factory!
In a traditional fertilizer factory with a capacity of 1-20 tons/hour, you may need approx. 20-40 workers across different stages of the fertilizer production line. Also, a typical team consists of equipment operators, workers, quality inspectors, maintenance staff, managers, electrical engineers, warehouse and logistics personnel. Because the fertilizer factory layout and production process often require human intervention, which drives up the labor costs.
How to Save Labor Cost of A Fertilizer Manufacturing Plant?
Actually, our company recommends upgrading to automated fertilizer production equipment. Although it may increase the initial investment in the fertilizer plant setup, it boosts productivity and reduces reliance on human labor, thereby lowering long-term operational costs. We equip our fertilizer production lines with automated systems. Moreover, these systems control raw material conveying, mixing, granulating, and packaging processes. Thus, the entire fertilizer production process becomes continuous and efficient, minimizing the need for human input at every stage. For example, you can use our belt conveyors with high automation degree. Because they connect each fertilizer processing stage with low energy consumption and eliminates the need for manual operation.
Additionally, you can further reduce labor costs by improving employee skills. You ought to train workers to have a variety of competencies. When one person can handle multiple processes, it decreases the transition time between different tasks and improves production efficiency in your fertilizer plant. To be honest, our equipment is easy to use. You just need to be familiar with which buttons control on our fertilizer equipment starting, stopping, and other functions. Furthermore, our engineers will guide you on how to use the equipment. We provide online video guidance or on-site training to ensure smooth operation of all your fertilizer manufacturing systems.
How Much Labor Cost Can You Save with Automatic Fertilizer Machinery?
By using our automatic equipment, your fertilizer factory can reduce the number of workers by 50%. So, you would only need 6-10 workers, including a loader operator, a raw material handler, two workers for packaging finished fertilizers, one mechanic and an electrician. If you purchase our fully-automatic packing machine and palletizing robot, you can eliminate more workers for auxiliary packaging and stacking finished products.
Additionally, labor costs vary by region, industry, job type, worker skills, and local economic levels. On average, the daily wage range for factory workers is about $5 to $150. By implementing automation, your fertilizer plant could save a significant amount on worker salaries. It can potentially reduce operational expenses by $30,000 to $200,000 or more annually, depending on your specific fertilizer plant layout.
Investing in Yushunxin fertilizer equipment can significantly reduce labor costs for your fertilizer factory. By automatic fertilizer production, you enhance productivity and lower the fertilizer plant cost over time. Our fertilizer production line simplifies operations and minimizes the number of workers needed.
Tips to Control Energy Consumption Cost in A Fertilizer Plant Investment
Energy costs represent a significant portion of a fertilizer plant’s operating expenses. Therefore, you can invest in energy-saving machinery from our company, such as crushers, mixers, and granulators, is driven by electricity. Energy costs represent a significant portion of a fertilizer plant’s operating expenses. Therefore, investing in energy-saving machinery is a valuable strategy. Our company recognizes that most fertilizer production equipment, such as crushers, mixers, and granulators, is driven by electricity. Electricity-powered machinery offers lower energy investment and no pollution, which reduces fertilizer production line costs. Electricity-powered machinery offers lower energy investment and no pollution, which reduces fertilizer production line costs.
In conclusion, controlling energy consumption costs significantly reduces overall fertilizer plant operating expenses. By investing in energy-efficient machinery, backup power solutions, and advanced granulation technologies, you can achieve higher production efficiency and long-term savings. Contact us to learn more about energy optimization strategies for your fertilizer factory setup.
How Much Does A Fertilizer Manufacturing Plant Cost to Acquire Raw Materials?
Since you have built up the fertilizer production workshop and determined the fertilizer manufacturing process, the next step is to consider the cost of raw materials. Thus, when it comes to this issue, you should not only compare the materials’ quality and price, but also think about transportation distance and costs.
Raw Materials’ Cost of Organic Fertilizer Production
If the customer owns a livestock farm, he can utilize abundant animal waste to make organic fertilizers. As a result, the cost of raw materials and transportation can be negligible. If not, you’d better to acquire them from the local farms and agricultural waste treatment plants. Due to the fairly cheap prices themselves, you can purchase in bulk.
Generally speaking, you have many options for organic fertilizer’s sources, such as livestock manure, agricultural residues, industrial waste, domestic waste, and urban sludge. However, sometimes you need to add certain amount of nitrogen, phosphorus and potassium substances, as well as the microbial agents to ferment for a period of time. So, it entails additional procurement costs. Certainly, you can use some practical materials to replace microbial agents like rice bran, yeast and sugar, etc.
Raw Materials’ Cost of Compound Fertilizer Production
Compound fertilizer contains two or more NPK elements, such as urea, MAP, SSP, calcium carbonate, KCL, potassium sulfate, etc. We suggest you should buy raw materials from suppliers. This is because the cost of concentrating and extracting them is often higher than the purchase price. Affected by supply and demand, seasons, transportation and other factors, raw material prices fluctuate substantially. Anyway, the specific situation relies on the local marketconditions.
In summary, when building a fertilizer plant, you need to carefully consider the various factors that affect its total cost from plant scale and capacity to raw material selection and equipment. These aspects play a role in determining the fertilizer manufacturing plant costs. If you require more specific price information, please let us know and we will provide you with the right solution and a free quote!
In summary, when building a fertilizer plant, you need to carefully consider the various factors that affect its total cost from plant scale and capacity to raw material selection and equipment. These aspects play a role in determining the fertilizer manufacturing plant costs. If you require more specific price information, please let us know and we will provide you with the right solution and a free quote!
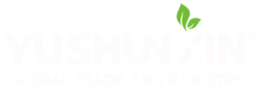
Get Free Quote Now!
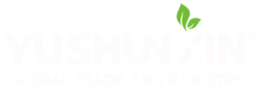